In-House Production of Key Parts Crucial to the Endless Quest for Improvement
Our aim is to produce the world's best medical endoscopes and endotherapy devices.
The components needed in order to do so are not always available on the market, and so in these cases we must create the components ourselves, starting with the development of materials and manufacturing facilities.
Through this endless cycle of finding our own solutions to problems, Olympus has built a global reputation based on a unique range of products.
This determination to produce key parts in-house remains an integral part of the Olympus manufacturing culture and is a vital source of the technology that gives our endoscopes and endotherapy devices the competitive edge.
Endless Drive to Improve Endoscope Insertion Technology
One of the most important requirements for endoscopes is the ability to access the targeted areas quickly and minimizing the discomfort to patients, and gastrointestinal endoscopes in particular must be able to traverse long and twisting lumina smoothly.
It is important to make the insertion tube of endoscopes designed for use in the upper digestive organs as thin as possible so as to facilitate insertion and minimize the effect on the patient. Inserting an endoscope into the large intestine is not a simple procedure, and access to deeper areas requires enhanced endoscope performance, combined with advanced skills on the part of the medical practitioner performing the procedure.
Endoscope manufacturers face two difficult tasks. First, is the need to facilitate endoscope insertion by making insertion tubes as thin as possible. Second, is the requirement of meeting the demands of medical practitioners concerning the design of insertion tubes. The development of insertion tubes that minimize patient stress while providing optimal operability for practitioners (bending, twisting, pushing, pulling) is an endless technological challenge.
If Parts are Unavailable on the Market, We Make them Ourselves
When Olympus first entered into the area of endoscope manufacturing, the technical expertise required for endoscopes was limited to design and lens production. Even if we had wanted to outsource endoscope components, there were no manufacturers making them or even interested in making them. So, in most cases, our only option was to make the components ourselves. This was the beginning of the development of our technology in this area. Needless to say, we were bound to face one obstacle after another. However, the necessity to do everything ourselves eventually worked to our advantage. This emphasis is reflected in the Olympus products of today. Olympus was determined to make all of the key components for endoscope insertion tubes in-house, including the tip parts with complex shapes, image guide made by bundling glass fiber, light guide fiber, bending section, bending rubber, and flexible connecting tube.
One of the most important components is a metal part attached to the tip of the endoscope. It has to be made from stainless steel to resist corrosion by highly acidic gastric juices. However, in the early 1960s there was no technology for cutting minute stainless steel components, and manufacturers specializing in cutting processes were unwilling to take on the task. Olympus painstakingly accumulated data by carrying out cutting tests to ascertain how final accuracy was affected by the type of steel used and the composition and the edge configuration of the cutting tools. Eventually we were able to develop technology for cutting stainless steel.
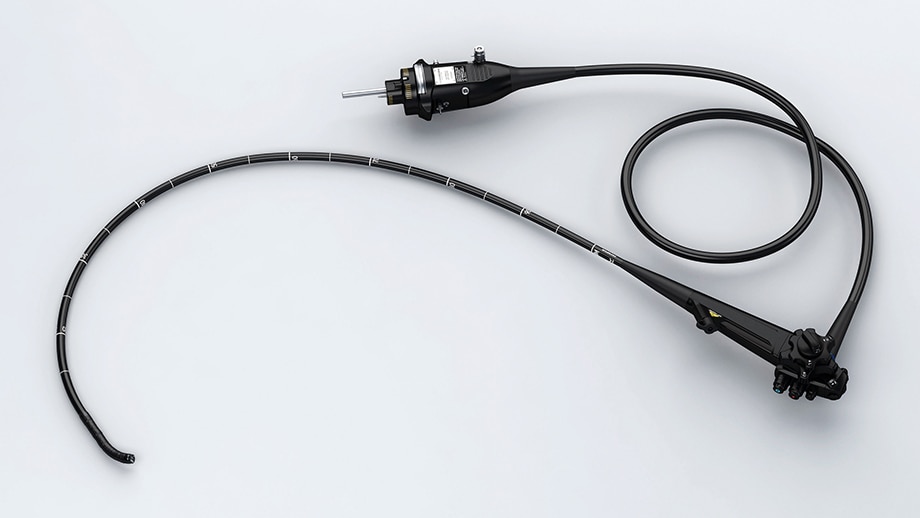
Medical endoscopes and gastrointestinal endoscopy scopes
Production of the connecting tube was initially outsourced, but medical practitioners were forever seeking improvements, and Olympus was determined to meet their expectations. Our staff made numerous visits to the manufacturer to ask for changes in the production method, but the manufacturer knew nothing about the practical use of the endoscopes and was reluctant to accommodate these requests. Olympus had direct access to the views of the end users in the medical community, and eventually we realized that only Olympus could create products that would reflect those wishes. We realized that we could not make superior products if we continued to rely on outside suppliers, so we canceled our contract with the manufacturer and began manufacturing the components in-house. We set our own quality standards, and through a process of trial and error we were able to develop our own process for manufacturing components that met our high standards.
One of the first processes to be brought in-house was plastic extrusion molding, which is an important factor for the ease of insertion. We went through a repeated cycle of trial-and-error, but we refused to abandon our continuing quest to improve insertability.
In the early 1990s, we achieved a dramatic breakthrough in the improvement of insertability when we succeeded in developing a continuous connecting tube with continuous flexibility. Furthermore, around 2007, we developed a high force transmission connecting tube, which smoothly transmits operations from the handle to the tip end of the connecting tube. Our quest to make even further improvements to the connecting tube continue to this day. Our aim is to develop a connecting tube that will make even more dramatic improvements in insertability.
Satisfy customer needs by stabilizing product quality and lowering costs
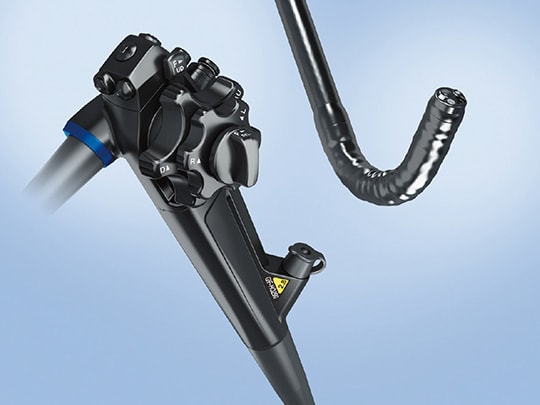
Scope operation part and tip part
Endoscopes and endotherapy devices require high-precision assembly technology with tiny components. Although this assembly was performed by hand up until then, due to the fineness of the work, the length of working time and variations in quality, there was no way we could satisfy our customers' needs.
Therefore, we aimed to resolve those issues by bringing together and automizing all the manufacturing know-how and technology we had cultivated until then.
With the vibrating unit, which is the key part for taking ultrasonic images, we joined together several hundred wires thinner than a hair with ultra-fine pitch. After developing an automatic machine for this work, we achieved reduced a working time and zero defects.
And, through in-house development of typical surgical instruments as disposable biopsy forceps and hemostatic clips, we also successfully automized all assembly processes and stabilized quality.
A Sense of Mission
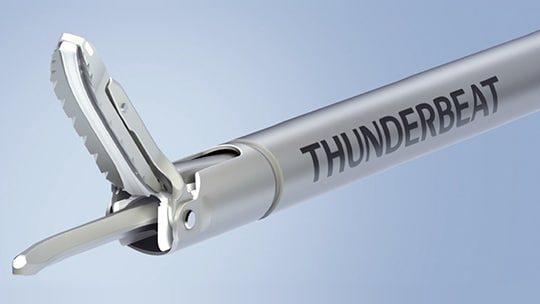
Surgical energy device tip part
Olympus has been involved in the development of endoscopes for more than half-a-century, but there is still room for improvement in our manufacturing technology. We are still determined to develop products that our competitors cannot match by continually moving ever closer to ideal performance characteristics through a process of non-stop enhancement.
Our production staff persevere in the creation of technology that will impress not only their development and design colleagues, but also ultimately the medical practitioners who use our products as well.
Our sense of mission and our pride tell us that "it is imperative that we manufacture our products by ourselves" and "we need to develop and improve endoscope and endotherapy device manufacturing technology through our own efforts".