Passing down Skills Backed by Finely Honed Instincts and Thorough Understanding of Basic Principles
Microscope manufacturing requires fastidious attention to detail and precision at every stage. This would not be possible without the finely honed instincts and diligence of highly skilled workers. The training of a highly skilled worker begins with an assessment of the skill level of that person.
He or she must then learn under the supervision of more experienced workers while constantly striving to understand and apply basic principles. Only someone who has made these efforts can truly be regarded as skilled. The most important assets in an Olympus manufacturing facility are our human assets. That is why it is so important to continue this tradition of excellence and skill from past to present, and from present to future.
* The Life Science Solutions and Industrial Solutions products are no longer owned or controlled by Olympus Corporation or part of its overall product portfolio. These products are being marketed, sold and distributed by Evident.
Our Founding Vision: To Measure Up to the Technology of German Microscope Manufacturers
Olympus was established as a manufacturer of microscopes. The founder of our company wrote a thirteen-year history of his relentless efforts to build his microscope manufacturing business. In this book, he offers the following reasons for the early success of Olympus.
A factory worker cannot acquire advanced and specialized skills overnight.
Many Japanese people seem to have good dexterity, and my experience indicates that this goes hand-in-hand with the manufacture of advanced precision optical equipment, especially microscopes. Every employee carries out research and manufacturing work, firmly believing that we Japanese have the capability to establish a position in the global playing field.
Though everyone recognized the superiority of advanced German products, no one could imitate the manufacturing methods and performance that made these products possible. With the existing processing equipment and adjustment methods it was extremely difficult, and endless cycles of experimentation and prototype production were required. The eventual success of Olympus in gaining recognition as a world-class microscope manufacturer was built on the advanced skills of those working in our production facility.
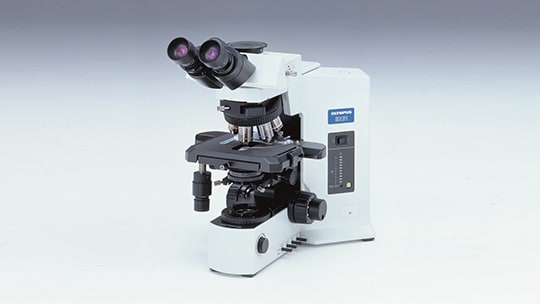
The BX51 research system micro-scope was a major success for Olympus.
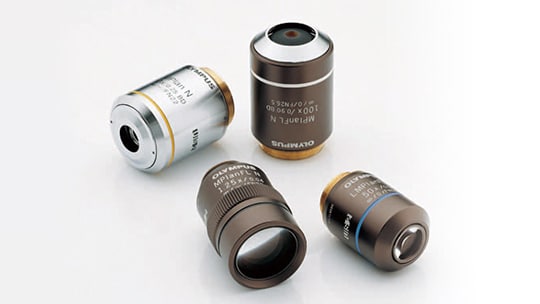
Objective lenses require ultra-precise adjustment.
Apprenticeship System-A Framework for the Succession and Accumulation of Skills
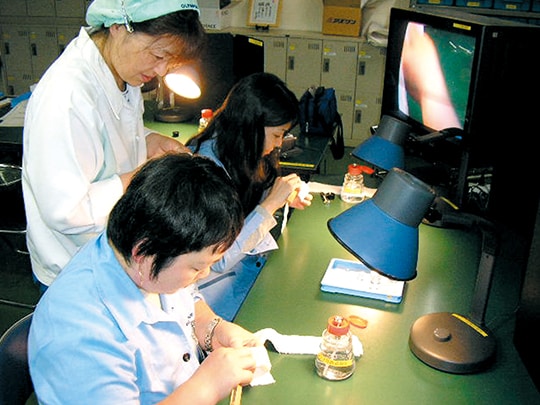
Highly skilled workers train their younger colleagues.
"There are masters at every manufacturing site, and various skills are passed down through the apprenticeship system. Olympus probably would not have been able to build our microscope manufacturing business without this imparting of knowledge by master workers.
"There are standards covering every process, from the machining of parts on down the line, but even if you produce parts that are within the standard tolerances, there will always be some variation, relative to the standard dimensions. This variation accumulates at the assembly stage, and the accumulation of these errors will be manifested as idiosyncrasies in the final product. We aim to achieve zero errors at the assembly stage, and even though parts are within the standard tolerances, they are not the same". These are the words of a highly skilled worker and recipient of the Yellow Ribbon Medal (a Japanese government award for people who have made exemplary contributions to industry).
He has compiled 80 pages of notes recording the know-how that he has accumulated through his decades of experience. He has carefully chronicled his day-to-day discoveries, failures, and lessons learned from the previous generation of workers. "The Yellow Ribbon Medal belongs to the factory, not to me," he says. He has imparted much of his knowledge to the next generation through his notes, although he and other senior workers still have much yet to teach.
Advanced Skills Evolve through Repeated Trial and Error Based on Firm Principles
Many master workers have learned their skills at the Ina Plant. A highly skilled worker, who was elevated to the status of master lathe operator in 2003, attributes his success to his on-going expo-sure to new technologies.
"The method we use to machine materials on a lathe or mill differs according to whether those materials have been cast or pressed. Through my work experience, I have learned to take note of the noise and heat generated during cutting, and I have gained the skill needed to machine parts to within micron-level accuracy".
When machining parts on a lathe, the operator needs to adjust the position of cuts to allow for the expansion caused by heat. Instinct alone is not enough at this level. He or she must determine the cutting conditions according to specific principles that include the calculation due to heat expansion.
A lens processor has tried to develop a grinding method based on a new elemental technology. He reached his own conclusion after numerous rounds of trial and error. "We considered and tried every available material and method when we determined the conditions for grinding, including the abrasives and pitch used, as well as the method used to prevent the lens from warping. We cannot achieve the optimum processing results if we are unable to predict the situation one minute from now or 30 minutes from now under given processing conditions".
Today, manufacturers in ever-increasing numbers are turning to processing machines with advanced computerized numerical control systems. As long as human operators are involved, though, there will always be a need for skilled workers. Without master operators, no manufacturing facility will be able to meet the changing needs of its customers. And true masters are always ready to teach younger workers and pass on their skills.
The Passing Down of Advanced Skills Stimulates Innovation
Olympus believes that people are an important asset for any manufacturer, and this philosophy is reflected in our "Technical Master" system, for instance . This system was first introduced at the Ina Plant as a way of developing and passing on the skills needed for microscope manufacturing. After passing numerous skill tests, the highly skilled workers ("Technical Masters") impart substantial amounts of knowledge to the next generation of workers through the machining of prototypes of the key components of a microscope. The "NC Machining Prototype Group" and "MC Machining Prototype Group" prototype component production lines that depend on these highly skilled workers are the perfect places for instruction.
To acquire advanced skills as quickly as possible, workers must first assess their present level of skill. Only then can they start to move closer toward the level achieved by their seniors. Older workers continue to cast a gentle eye on the newcomers as the latter endeavor to become skilled workers in their own right. Skills handed down through the long history of Olympus have also helped to stimulate technological innovation. Highly skilled workers use their knowledge to rise to the challenge of reaching new levels of quality. Production technology is complemented by advanced skills, and the organic linkage between them helps to drive progress toward increasingly sophisticated products.
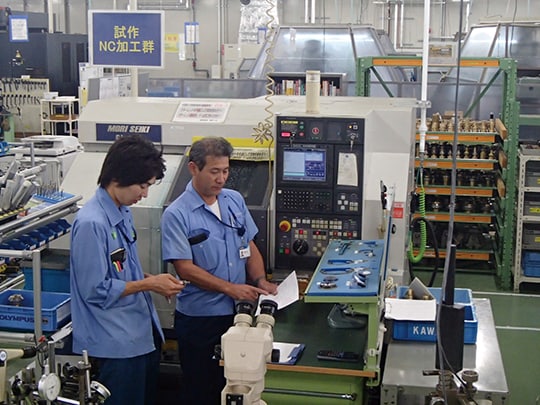
Imparting know-how to the next generation of highly skilled workers in the NC Machining Processing Group.
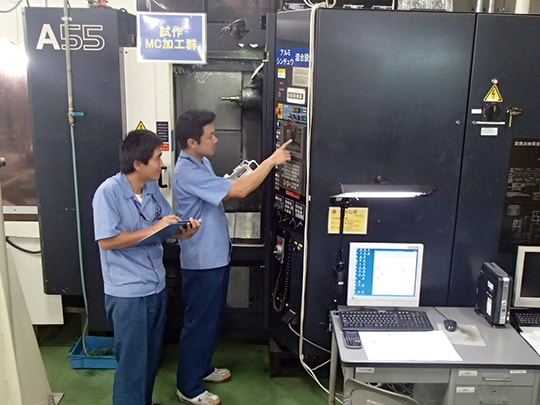
Highly skilled worker teaching know-how in the MC Machining Prototype Group.